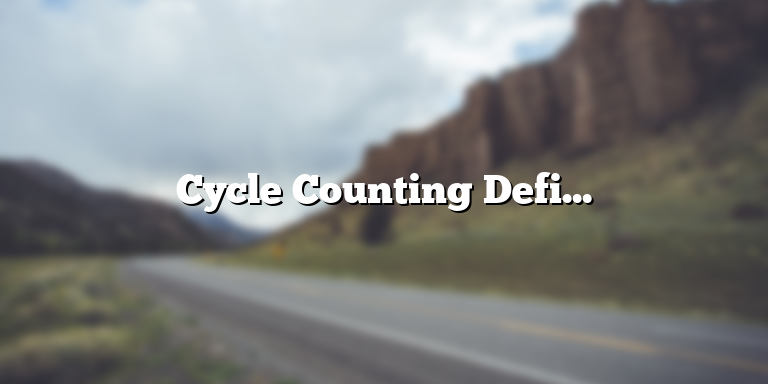
Cycle Counting Definition
Cycle counting is a crucial inventory management technique that involves regularly counting a subset of your inventory. It is a highly effective inventory control process that enables you to maintain the accuracy of your inventory records, minimize discrepancies between inventory levels, and stay up-to-date with your stock levels. By identifying and correcting any errors or inconsistencies in your inventory records, cycle counting helps you to make better-informed decisions and improve the overall efficiency of your warehouse operations.
Cycle counting is an ongoing process that involves counting a small portion of your inventory on a regular basis. This approach is in contrast to the traditional method of conducting an annual physical inventory where the entire inventory is counted at once. Instead, cycle counting requires you to count a small percentage of your inventory frequently, typically on a daily or weekly basis. The frequency of the cycle count depends on the type of inventory, the volume of transactions, and the nature of the business.
The cycle counting process involves selecting a subset of inventory items to be counted, based on a predefined criteria. The items to be counted may be chosen randomly, or based on criteria such as value, demand, or sales volume. The inventory counts are then compared to the existing inventory records, and any discrepancies are recorded and investigated. This helps to identify any issues, such as theft, damage, inaccurate data entry, or poor inventory management processes.
Cycle counting is designed to identify errors and discrepancies in a timely manner, allowing corrective action to be taken before they become significant problems. By counting inventory frequently, you can quickly and easily determine whether any discrepancies exist, and take steps to resolve them before they lead to lost sales or customer dissatisfaction. In contrast, an annual physical inventory may not identify discrepancies until long after they have occurred, making it difficult to take corrective action in a timely manner.
Cycle counting offers numerous benefits over the traditional annual physical inventory. It allows you to maintain a more accurate inventory record, minimize discrepancies and losses, and improve warehouse efficiency. It also reduces the amount of time and resources required to conduct a physical inventory, as well as the disruption to normal business operations. By adopting cycle counting as part of your inventory management strategy, you can ensure the accuracy and efficiency of your warehouse operations, leading to improved profitability and customer satisfaction.
The Purpose of Cycle Counting
Cycle counting is an inventory management technique that involves regularly counting a small portion of inventory on hand at a time, as opposed to conducting a physical inventory count of all inventory at once. This technique helps to maintain inventory accuracy and reduces the need for time-consuming physical inventory counts. The purpose of cycle counting is to ensure that inventory records accurately reflect the actual quantity of goods on hand, which in turn helps to minimize stockouts, reduce excess inventory, and improve overall supply chain efficiency.
The main goal of cycle counting is to identify and correct inventory discrepancies in a timely manner before they become major problems. Cycle counting is an ongoing process that involves counting a predetermined subset of inventory on a regular basis, typically daily, weekly, or monthly, depending on the size of the warehouse and the volume of goods stored. By counting a small portion of inventory regularly, warehouses can detect inventory errors and resolve them before they escalate into larger issues that require a complete physical inventory count.
Cycle counting can be customized to fit the specific needs of each business. For examples, some businesses may choose to only cycle count high-value items or items that have a high movement rate, while others may choose to cycle count all items in their inventory. The frequency of cycle counting can also be adjusted based on the level of risk associated with inventory discrepancies and the level of resources available for conducting regular counts.
The key benefit of cycle counting is that it provides a more accurate picture of inventory levels in real-time. This helps businesses to optimize their inventory levels, reduce carrying costs, minimize the risk of stockouts, and improve overall customer satisfaction. By having accurate inventory levels, businesses can make more informed decisions about when to reorder, how much to order, and where to store excess inventory. This helps to improve inventory turnover rates and reduce the amount of money tied up in excess inventory.
Cycle counting also helps businesses to maintain a high level of inventory accuracy by identifying discrepancies early on, which allows them to take corrective action before inventory records become significantly inaccurate. This helps to minimize errors and improve overall inventory management efficiency. By regularly reviewing inventory counts, businesses can identify trends, track performance, and make data-driven decisions to improve operations and reduce costs.
In conclusion, cycle counting is an essential inventory management technique that helps businesses to maintain inventory accuracy, increase efficiency, and reduce costs. By counting a small portion of inventory on a regular basis, businesses can identify and correct inventory discrepancies before they become larger issues that require a full physical inventory count. Cycle counting can be customized to fit the specific needs of each business and can be adjusted based on the level of risk associated with inventory discrepancies and the level of resources available for conducting regular counts. By implementing cycle counting techniques, businesses can optimize their inventory levels, reduce carrying costs, and improve overall supply chain efficiency.
Cycle Counting Process
Cycle counting, also known as spot checking or partial inventory checking, is a process of inventory control that helps you maintain accurate stock counts without disrupting normal business operations. Cycle counting allows you to monitor and correct discrepancies in your inventory records by counting a small portion of inventory regularly and frequently, rather than counting all items at once.
Benefits of Cycle Counting
The use of cycle counting comes with several benefits, including:
- Improved Accuracy: Cycle counting helps maintain the accuracy of inventory records by regularly checking counts and correcting discrepancies. It ensures that inventory counts are always up-to-date and accurate, giving you a clear view of stock levels and preventing stockouts or overstocking.
- Efficient: Unlike other inventory counting methods that interrupt normal business operations, cycle counting is a non-intrusive inventory control method that can be done without disrupting normal operations. The frequency of the cycle count depends on the size of your inventory, but it typically takes less time than a full physical inventory count.
- Cost Savings: Cycle counting helps reduce inventory holding costs by ensuring that inventory levels are always optimized. By maintaining accurate inventory levels, you can reduce the risk of overstocking, improve cash flow, and prevent unnecessary carrying costs.
The Cycle Counting Process
The cycle counting process involves several steps. Here is a step-by-step guide on how to conduct cycle counting in your business:
- Select Inventory to Count: The first step is to select a specific subset of inventory to count. This can be done by dividing your inventory into smaller groups based on SKU, location, category, or any other criteria.
- Set the Counting Method: You can use different counting methods, such as visual inspection, barcode scanning, or manually counting, for the selected items.
- Count the Selected Items: Count the selected items using the chosen counting method and record the quantity counted on a count sheet or electronically. It’s important to ensure that the person conducting the count is well-trained to avoid errors.
- Compare Count with Record: Compare the counted quantity with the inventory record to identify any discrepancies. Investigate and resolve any discrepancies identified.
- Adjust Inventory Record: Once the discrepancies have been resolved, adjust the inventory record to reflect the correct counts.
- Repeat Process: Repeat the process regularly, depending on the size of your inventory and the frequency of demand.
Conclusion
Cycle counting is essential for any inventory management system. By regularly and frequently counting a small subset of inventory, you can maintain an accurate inventory count without disrupting normal business operations. This helps reduce inventory holding costs, prevent stockouts or overstocking, and improve the efficiency of your inventory management. By following the cycle counting process, you can ensure that you always have an accurate and up-to-date inventory count.
Frequency of Cycle Counting
Cycle counting is an inventory management technique used to ensure inventory accuracy and avoid stockouts and overstocking. It involves counting a subset of inventory on a regular basis to identify discrepancies and correct them before they result in inventory errors. One important aspect of cycle counting is the frequency at which it should be done.
The frequency of cycle counting depends on several factors such as the value, activity, and criticality of your inventory. If your inventory is high-value or fast-moving, it may require more frequent cycle counting to ensure accuracy. On the other hand, low-value or slow-moving inventory may not require frequent cycle counting.
Cycle counting frequency also depends on how critical inventory accuracy is to your business. If inventory errors can result in significant costs or losses, you may need to perform cycle counting more frequently to mitigate potential risks.
In general, it is recommended to perform cycle counting at least once a year. This ensures that your inventory accuracy is being reviewed and corrected on a regular basis. However, some businesses may need to perform cycle counting on a more frequent basis, such as monthly or quarterly.
It is important to note that the frequency of cycle counting may vary for different inventory items or locations. For example, high-value items or high-risk locations may require more frequent cycle counting than low-value items or low-risk locations.
Regardless of the frequency chosen, it is important to have a consistent cycle counting schedule to ensure accuracy and reliability. This can help prevent stockouts, overstocking, lost inventory, and other inventory issues that can negatively impact your business.
In summary, the frequency of cycle counting should take into account the value, activity, and criticality of your inventory. While it is recommended to perform cycle counting at least once a year, businesses may need to perform it more frequently based on their unique inventory needs. Consistency in cycle counting scheduling is key to ensuring accurate and reliable inventory management.
Benefits of Cycle Counting
When it comes to warehouse inventory management, accuracy is key. Inaccurate inventory counts can result in excess stock, increased carrying costs, and stockouts that can lead to lost sales and poor customer satisfaction. Cycle counting is an inventory management strategy that can help prevent these issues by regularly counting a portion of your inventory at predetermined intervals. Here are the top benefits of cycle counting:
1. Boosts inventory accuracy
Cycle counting helps verify inventory accuracy by systematically counting a portion of inventory. Instead of shutting down operations for a full physical inventory count, cycle counting enables you to verify the accuracy of inventory records in real-time. This ensures that you have an accurate count of your inventory levels and can make data-driven decisions about stock levels and ordering.
2. Reduces time and labor costs
Cycle counting reduces the time and labor costs associated with a full physical inventory count. Instead of shutting down the warehouse for an entire day, cycle counting can be completed in shorter intervals over time. This allows you to maintain operations while preventing the need for a full inventory shut down. By spreading the process out over several days, you can also reduce the labor costs associated with a full physical inventory count.
3. Identifies discrepancies earlier
Since cycle counting is performed regularly, discrepancies can be identified earlier. This can help prevent minor issues from becoming larger problems over time. When discrepancies are identified sooner, you can take action to correct the issue before it becomes more serious. This can help maintain inventory accuracy and prevent issues down the line.
4. Prevents stockouts
Cycle counting helps maintain accurate inventory levels, which can prevent stockouts that can harm customer satisfaction. By regularly verifying inventory accuracy, you can ensure that you always have the right stock levels to meet demand. This can help prevent stockouts, which can lead to lost sales and poor customer satisfaction.
5. Improves decision making
Cycle counting provides you with accurate and timely inventory data, which can be used to make more informed decisions about your inventory and operations. This data can be used to optimize stock levels, improve supply chain efficiency, and reduce carrying costs. By having accurate inventory data, you can make data-driven decisions that can help improve the overall efficiency of your warehouse operations.
In conclusion, cycle counting is an effective inventory management strategy that can help maintain inventory accuracy, reduce time and labor costs, identify discrepancies earlier, prevent stockouts, and improve decision-making. By implementing cycle counting into your warehouse operations, you can ensure that your inventory records are accurate, and make data-driven decisions that can help improve the efficiency of your operations.
Pitfalls to Avoid
Cycle counting is an effective inventory management technique that allows businesses to reconcile discrepancies, reduce errors, and maintain accurate inventory records. However, despite its benefits, cycle counting can be a complex process that requires careful planning and execution. Here are some pitfalls to avoid when implementing a cycle counting program:
1. Lack of Preparation
Cycle counting is a time-sensitive process that needs proper preparation and planning. Before starting a cycle counting program, businesses must ensure that they have enough resources, including trained personnel, accurate data, and proper equipment. Lack of preparation can lead to inaccurate counts, wasted time and resources, and ultimately undermine the effectiveness of the cycle counting program.
2. Inadequate Training
Cycle counting requires well-trained personnel who have a clear understanding of the process and the inventory management system used by the business. Inadequate training can lead to errors, delays, and inaccurate counts. It is important to provide proper training to all personnel involved in the cycle counting process, including warehouse employees, supervisors, and managers.
3. Over-reliance on Automation
Automation and technology can streamline the cycle counting process, but they should not be relied upon entirely. Human involvement is essential to ensure that the inventory records are accurate, and any discrepancies and errors are resolved promptly. Over-reliance on automation can lead to complacency and errors that can undermine the cycle counting program’s effectiveness.
4. Inaccurate Data
Inaccurate data is one of the most significant causes of errors in cycle counting. Before starting a cycle counting program, businesses must ensure that their inventory records are up-to-date and accurate. Inaccurate data can lead to over-counting or under-counting of inventory, resulting in lost revenue and reduced customer satisfaction.
5. Inconsistent Procedures
Consistent procedures are crucial to ensure accuracy and reliability in the cycle counting process. Inconsistent procedures can lead to confusion, errors, and wasted time and resources. Businesses must ensure that their cycle counting procedures are clearly defined, communicated, and followed consistently.
6. Failure to Analyze Results
Analysis of cycle counting results can provide valuable insights into the effectiveness of the inventory management system and identify areas for improvement. Failure to analyze results can undermine the cycle counting program’s effectiveness and lead to missed opportunities. Businesses must ensure that they analyze cycle counting data regularly and use the insights gained to improve their inventory management system.
In conclusion, cycle counting is a crucial inventory management technique that can help businesses maintain accurate inventory records and improve their overall efficiency. However, businesses must be vigilant and avoid the pitfalls that can undermine the effectiveness of the cycle counting program. By ensuring proper planning, preparation, training, and analysis of results, businesses can reap the benefits of a successful cycle counting program.
Tools for Cycle Counting
When it comes to cycle counting, leveraging the right tools and technologies can make a huge difference in the accuracy and efficiency of your inventory management process. With the help of automated inventory management systems, barcode scanning tools, and other technological advancements, businesses can streamline their cycle counting operations and reduce the risk of human error.
Automated inventory management systems are designed to track and manage inventory levels on a real-time basis, allowing businesses to keep a close eye on their stock levels and take proactive measures to avoid stockouts and overstocking. These systems use advanced algorithms to predict demand and automatically reorder products when stock levels fall below a certain threshold. By integrating these systems with their cycle counting process, businesses can ensure that they always have an accurate view of their inventory levels, reducing the risk of stock discrepancies and improving the accuracy of their financial reporting.
In addition to automated inventory management systems, barcode scanning tools can also help improve the efficiency of the cycle counting process. By scanning barcodes on products and tracking their movements in real-time, businesses can gain a better understanding of their inventory levels and identify any discrepancies or irregularities. Barcode scanning tools can also be used to track the movement of products across different locations or warehouses, making it easier to keep track of inventory across a distributed supply chain.
Another tool that businesses can use to improve their cycle counting process is RFID (Radio Frequency Identification) technology. RFID tags can be attached to products or shipping containers, allowing businesses to track the location and movement of their inventory in real-time. This can be particularly useful for businesses that deal with high volumes of inventory or operate distribution centers across multiple locations. RFID technology can help businesses reduce the time and effort required for cycle counting, while also improving the accuracy of their inventory management process.
Overall, the right tools and technologies can make a huge difference in the accuracy and efficiency of your cycle counting process. By leveraging automated inventory management systems, barcode scanning tools, RFID technology, and other technological advancements, businesses can streamline their operations, reduce the risk of human error, and gain a more accurate view of their inventory levels. Whether you’re a small business looking to improve your inventory management process or a large enterprise with complex supply chain requirements, investing in the right tools for cycle counting can help you achieve your inventory management goals and stay ahead of the curve in today’s rapidly evolving business landscape.