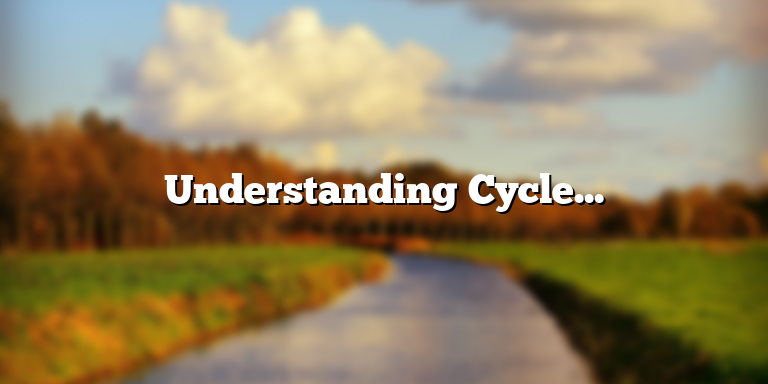
Cycle Counts Definition
Cycle counts are a fundamental aspect of inventory management in the supply chain industry. In essence, cycle counts refer to the process of routinely counting a small subset of inventory items on a regular basis. The objective of cycle counts is to compare the quantity of inventory physically counted against the quantity of inventory recorded in the system.
While physical counting of inventory may seem like an obvious requirement, it is essential to do so. This is because even minor discrepancies in inventory records can lead to significant consequences, such as overstocking, stockouts, and inaccurate cash flow. Running regular cycle counts ensures these discrepancies can be identified and rectified before they become major issues.
Traditionally, physical inventory counts were conducted periodically, usually once or twice a year, and required significant resources to implement. However, cycle counts have replaced traditional inventory counting methods as they are less time-consuming, more accurate, and can be done in-house on a continuous basis. These days, companies try to incorporate cycle counts as part of their management system to ensure that the inventory levels remain accurate and updated as per the records.
One of the significant benefits of cycle counts is that it helps in identifying the cause of the discrepancies. With regular cycle counts, inventory discrepancies can be promptly identified, and corrective action taken to ensure that the inventory records remain accurate. Additionally, the process provides insight into inventory trends, and it fosters a culture of accuracy and responsibility around inventory management.
Conducting cycle counts requires a lot of planning and preparation to be successful. Most companies find it useful to classify their inventory into different categories based on value, velocity, and ABC analysis. High-value or fast-moving inventory items should be counted more regularly than low-value or slow-moving ones. Regular cycle counts ensure that discrepancies are identified quickly and rectified before becoming significant issues.
It is also necessary to have an inventory management system that can track inventory movement and how inventory is received, disbursed, and adjusted. With a robust inventory tracking system, cycle counts can be conducted with ease, and discrepancies will be identifiable at the earliest. Furthermore, warehouse management systems can automate the cycle counting process, which streamlines the inventory counting process and makes life easier for staff that would typically be involved in inventory counts.
In conclusion, cycle counts are a vital aspect of inventory management that can benefit businesses of all sizes and types. Regular cycle counts can ensure that inventory levels remain accurate, discrepancies can be identified and rectified promptly, and costs associated with overstocking or stockouts can be avoided. By conducting cycle counts, companies can focus on improving their inventory control, organization, and management, thereby improving performance and profitability.
When Should Cycle Counts Be Performed?
Cycle counts should be performed frequently to maintain accurate inventory records and to prevent inventory errors. Generally, companies perform cycle counts on a regular basis throughout the year in addition to conducting an annual physical inventory count. The frequency of cycle counts depends on the type of inventory, the accuracy of inventory records, and the level of activity. For example, high-volume items that have frequent transactions should be counted more often than low-volume items.
Companies can either perform cycle counts continuously or on a defined schedule. Continuous cycle counting involves counting a small portion of inventory daily or weekly. This method is useful for high-volume items that require frequent monitoring. On the other hand, scheduled cycle counting involves counting a specific group of items on a predetermined schedule. This approach is more time-efficient and is suitable for low-volume items that do not require constant monitoring.
When scheduling cycle counts, companies should consider factors such as seasonality, sales patterns, and lead times. For example, if a company sells Christmas decorations, it may schedule more frequent cycle counts during the holiday season due to increased demand. Similarly, if a company has a long lead time for a particular item, it may schedule more frequent cycle counts to ensure that the item is always in stock.
In addition, companies should perform cycle counts whenever there is a significant change in inventory levels. For example, cycle counts should be performed when new inventory arrives, when inventory is transferred between locations, or when inventory is damaged or lost. These counts help to ensure that inventory records are up-to-date and accurate.
Overall, cycle counts should be performed regularly to maintain accurate inventory records and to prevent inventory errors. By implementing a cycle counting program, companies can improve inventory accuracy, reduce carrying costs, and increase customer satisfaction.
How to Prepare for a Cycle Count
Cycle counts are one of the most important inventory management procedures every business needs to undertake. Proper cycle counting ensures that the inventory is accurate, and the business can make informed production and procurement decisions. To achieve accurate cycle counts, you need to prepare adequately. Here are some steps to follow when preparing for a cycle count:
Create a Schedule
One key aspect of preparing for a cycle count is creating a schedule. The schedule should capture the time when the count will happen, how long it will take, and the people involved. The schedule should also consider the business’s peak periods to ensure that it does not interfere with daily operations. Once the schedule is in place, ensure that everyone involved understands the timeline and the importance of adhering to the schedule.
Identify Items to be Counted
The next critical step is to identify the items to count. Ensure that you have a comprehensive list of all the inventory items, their locations, and their description. This list will guide the counting process and ensure that the inventory is accurate. This is also an excellent time to dispose of obsolete stock and identify any missing items. By identifying the items, you will avoid counting items twice or missing some items altogether.
Ensure Inventory is Accessible
Finally, ensure that the inventory is accessible. The inventory location should be clean, well-lit, and organized for easy counting. Some items may be on the top shelf, which may require the use of ladders or other specialized equipment. Ensure that you have all the necessary equipment and tools to make the inventory accessible. This will speed up the counting process and ensure accuracy.
Conclusion
Cycle counting is an essential part of every inventory management procedure. Proper preparation ensures that the process is smooth, fast and avoids errors. By following the steps outlined above, you will be adequately prepared for a cycle count. Remember, the accuracy of the inventory is critical and can directly impact the business’s operations and profitability. Therefore, investing in robust cycle counting procedures is a wise business decision.
How to Conduct a Cycle Count
Cycle counts are conducted to ensure that a company’s inventory records are accurate. By conducting regular cycle counts, companies can identify discrepancies in their inventory records early, reducing the chances of stockouts, overstocks, or other inventory-related problems. Here are the steps to effectively conduct a cycle count:
1. Determine the Items to be Counted
The first step in conducting a cycle count is to determine which items will be counted. You can choose to count a small portion of your inventory or count each item. Companies often set a schedule for counting specific items, and this can be done based on factors such as item value, demand, and velocity. By prioritizing items, you can ensure that high-value or fast-moving items are counted more frequently than less critical items.
2. Choose a Counting Method
Once you have determined which items to count, you need to choose a counting method. The two primary methods of counting are manual and electronic. Manual counting is performed by physically counting each item while electronic counting involves using technology to count items such as RF scanners or barcode readers.
3. Prepare for the Count
Before starting to count, it is essential to prepare the inventory. This can include organizing the warehouse, clearing any obstructions, and ensuring that the items are easy to access. You also need to ensure that the counting team has all the necessary tools such as clipboards, pencils, and scanning devices.
4. Conduct the Count
The actual counting process involves physically counting each item according to its location. It is essential to ensure that each item is counted accurately, and any discrepancies identified during the count are noted down. If there are any items that cannot be located, the supervisor must be informed so that corrective action can be taken.
It is also crucial to follow an established count procedure to ensure that the process remains consistent. For example, the counting method, the number of items to be counted, and the order in which they are counted should remain the same for each cycle count.
In Conclusion
Cycle counting is a critical process that helps businesses maintain accurate inventory records. Conducting cycle counts regularly can help identify inaccuracies in recording inventory levels, helping to minimize stock issues throughout the supply chain. By following the correct procedures and methods, companies can ensure that their inventory levels are always accurate, reducing costs and increasing efficiency in the process.
What Are the Benefits of Cycle Counts?
Cycle counts are a valuable inventory management tool that can help businesses stay organized, maintain accurate inventory records, and prevent stockouts. By conducting regular cycle counts, companies can identify discrepancies in their inventory levels and make adjustments to ensure that stock levels are always where they need to be. Here are some of the key benefits of cycle counts:
1. Prevent Stockouts
One of the primary benefits of cycle counts is that they can help businesses prevent stockouts. By regularly monitoring inventory levels, companies can quickly identify when stock is running low and order more before it runs out completely. This can help ensure that customers are always able to purchase the products they need, without experiencing frustrating delays or out-of-stock situations.
2. Reduce Carrying Costs
Cycle counts can also help businesses reduce carrying costs by ensuring that they only keep as much inventory on hand as they need. By regularly adjusting inventory levels based on actual demand, companies can avoid over-ordering and free up valuable storage space. This can help save money on warehouse space and reduce the risk of spoilage, damage, or obsolescence.
3. Identify Inventory Inaccuracies
Another key benefit of cycle counts is that they can help businesses identify inventory inaccuracies early on. By comparing actual inventory levels to what the company thinks it has on hand, businesses can quickly identify discrepancies and investigate the root causes. This can help prevent future miscounts, reduce errors, and improve the efficiency of the inventory management process overall.
4. Improve Reconciliation Processes
When cycle counts are conducted regularly and accurately, they can help businesses improve their reconciliation processes. By reconciling physical inventory levels with what is recorded in the accounting system on a regular basis, companies can reduce errors and improve the accuracy of their records. This can help make it easier to identify and correct discrepancies, and provide a more complete picture of the company’s financial health.
5. Enhance Customer Satisfaction
Ultimately, cycle counts can help businesses enhance customer satisfaction by improving the accuracy of their inventory records and preventing stockouts. When customers can purchase the products they need when they need them, they are more likely to be satisfied and loyal to the company. This can help increase sales, reduce costs associated with lost customers, and improve the overall reputation of the business.
In conclusion, cycle counts are an essential element of effective inventory management. By regularly monitoring inventory levels and making adjustments based on actual demand, companies can prevent stockouts, reduce carrying costs, identify inventory inaccuracies, improve reconciliation processes, and enhance customer satisfaction. For businesses looking to optimize their inventory management practices, cycle counts are a must.
How to Analyze Cycle Count Data
Let’s start with a quick reminder of what cycle counting is. It’s a method of inventory control that entails counting a small portion of inventory regularly. The purpose of cycle counts is to maintain an accurate count of inventory levels, uncover discrepancies, and prevent inventory shrinkage.
When analyzing cycle count data, there are several steps you can take to ensure that you’re doing it effectively. Here are five essential steps:
1. Identify Discrepancies
The first step in analyzing cycle count data is identifying discrepancies. This means comparing the actual count with the expected count. If there is a discrepancy, you need to investigate why and what caused it. For example, was the discrepancy caused by a miscount or a misplaced item? Was there a problem with the product itself or the storage location? Identifying the source of discrepancies is the first step in effective analysis.
2. Investigate the Root Cause
Once you’ve identified discrepancies, the next step is to investigate the root cause. Understanding what caused the discrepancy is essential to improve accuracy going forward. To accomplish this, you should look at any patterns that may exist. Are there areas within the warehouse where discrepancies occur more frequently? Is there a particular type of product that’s causing more issues than others? Investigating the root cause will help you understand where the problem lies and take action to rectify it.
3. Make Necessary Adjustments
Once you’ve identified the discrepancies and investigated their root cause, the next step is to make the necessary adjustments. This includes updating records, making corrections to inventory levels, and recalibrating processes if needed. You should also make sure that any new processes or changes to existing ones are communicated to the relevant personnel.
4. Prioritize High-Value Items
A smart approach is to prioritize high-value items when it comes to cycle counting. These are products that have a higher value or make up a significant portion of the inventory. Cycle counting high-value items regularly ensures that there is accurate tracking and reduces the potential for inventory shrinkage. It also minimizes disruptions to regular business operations, such as delays in fulfilling orders.
5. Use Technology Where Possible
Finally, technology can be an excellent tool when analyzing cycle count data. There are many inventory management software solutions available that can help automate the counting process. With real-time data available, it is easier to spot discrepancies and root causes quickly. These software solutions can also track inventory levels over time, make any necessary adjustments and provide valuable insights that can improve overall warehouse efficiency.
In conclusion, analyzing cycle count data is a critical process that ensures accurate inventory levels. By following these steps and using technology where possible, you can improve accuracy, reduce discrepancies, and ultimately help your organization save time and money.
What Are the Best Practices for Cycle Counts?
Cycle counts are a critical part of inventory management. They are regular physical counts of a portion of inventory that allows businesses to identify and correct any discrepancies in inventory records. To ensure that cycle counts are effective and efficient, there are some best practices that businesses should follow.
Select Appropriate Items to Count
The first step in effective cycle counts is to choose the appropriate items to count. It is essential to prioritize items that are critical to the operation of the business and have a high or low turnover rate. By focusing on these items, businesses can better identify discrepancies and ensure that inventory levels are accurate.
In addition to prioritizing items, businesses should also consider grouping items by location, size, or value. This approach can help to streamline the counting process and reduce the time and effort required to complete the count.
Set Realistic Count Targets
Setting realistic count targets is essential to achieving effective cycle counts. Targets should be based on the volume of inventory, the size of the facility, and the number of employees involved in the counting process.
By setting realistic targets, businesses can ensure that the cycle count process is manageable, and employees are not overwhelmed. This can also help to reduce the risk of errors or inaccuracies that can result from rushing the counting process.
Involve Employees in the Process
Another critical best practice is to involve employees in the cycle count process. Employees are more likely to take ownership of the inventory and ensure its accuracy if they are involved in the counting process. This also helps to promote a culture of accountability and transparency within the organization.
Employees can also provide valuable insights into the inventory, such as identifying trends or issues that may have gone unnoticed by management. By involving employees in the process, businesses can improve the accuracy of their inventory records and promote a sense of teamwork and collaboration within the organization.
Conclusion
Effective cycle counts are essential to maintaining accurate inventory records and improving the overall performance of the business. By selecting appropriate items to count, setting realistic count targets, and involving employees in the process, businesses can ensure that their cycle counts are efficient, accurate, and effective. Implementing these best practices can help businesses to save time, reduce costs, and improve their bottom line.