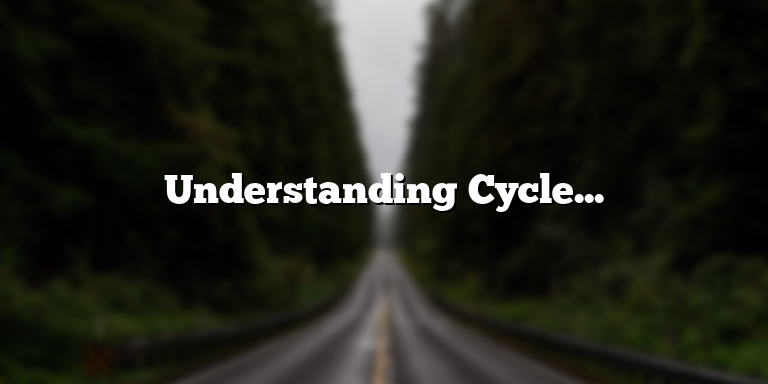
Definition of Cycle Count
Cycle count is a commonly used practice in inventory management that involves regular counting of a portion of inventory items to monitor and maintain accurate inventory levels. It is a cost-effective method to keep track of inventory, detect discrepancies, and make data-driven decisions to improve the bottom line.
Cycle counts offer a proactive approach to inventory management, making it easier to detect and resolve any issues before they snowball into bigger problems. By regularly counting a subset of inventory items on a rolling basis, businesses are better equipped to prevent stockouts, overstocking, and losses due to shrinkage.
This method provides an ongoing snapshot of inventory accuracy, allowing businesses to identify patterns and make necessary adjustments to their inventory management practices. By implementing cycle counts, businesses can reduce the need for time-consuming and costly physical inventory counts, which can disrupt daily operations.
The Importance of Cycle Counts
Cycle counts are critical to maintaining accurate inventory levels, especially for businesses that deal with a high volume of products. Manual inventory counts can be both time-consuming and inaccurate, leading to miscounted stock, which can trigger a chain reaction of problems.
Cycle counts can help businesses prevent stockouts or overstocking, reducing the likelihood of spoilage or obsolescence. Additionally, these practices can provide a clear understanding of inventory trends, making it easier to optimize replenishment processes and minimize the costs associated with carrying inventory.
By regularly counting inventory items in smaller batches, businesses can identify discrepancies and respond quickly, reducing the probability of making wrong decisions based on inaccurate data.
The Process of Cycle Counts
The first step in implementing a cycle count program is to create a plan customized for the needs of your business. This plan should include the frequency of counts, the selection of inventory items to be counted, and the count procedures.
Typically, businesses choose to count inventory every day, week or month. The frequency depends on the nature of the items, the volume of products, and the available resources. Inventory items are selected randomly or based on their categorization, such as high-value items or items that move quickly.
Once the items are identified, count sheets are created, and inventory counts are conducted. The results are then compared to the inventory record in the system, and any discrepancies are identified, explained, and corrected accordingly.
Lastly, cycle counting results are shared with relevant personnel, and any necessary actions are taken to improve inventory accuracy.
Conclusion
Cycle counts are an essential tool for businesses of all sizes to maintain inventory accuracy and optimize their inventory management practices. By implementing cycle counts correctly, businesses can prevent unnecessary stockouts and overstocking, reduce costs, and improve decision-making processes based on accurate data.
Overall, cycle counts are crucial to keep inventory management processes running smoothly. By focusing on a smaller subset of inventory on an ongoing basis, cycle counting helps to minimize the possibility of incorrect inventory counts, and reduce the need for costly and time-consuming manual inventory counts.
Why Do Companies Use Cycle Counts?
Inventory accuracy is critical to the success of a business. For this reason, many companies use cycle counts as a method of ensuring accuracy. A cycle count is a method of inventory control that involves counting a small subset of inventory at regular intervals. By counting a smaller portion of the inventory, cycle counts can be completed more quickly and easily than a full inventory audit.
But why does a company need to use cycle counts in the first place? There are several reasons:
Reason 1: Reduce Shrinkage
Shrinkage is the term used to describe the loss of inventory due to theft, damage, or other factors. Shrinkage can have a significant impact on a company’s bottom line. According to the National Retail Federation, shrinkage accounts for more than $50 billion in losses annually for US retailers.
Cycle counts can help companies identify and address shrinkage. By regularly counting inventory, companies can identify discrepancies between the actual inventory on hand and the inventory listed in their records. This allows companies to investigate and address potential issues before they become serious problems.
Reason 2: Improve Supply Chain Efficiency
Inventory accuracy is also critical for ensuring supply chain efficiency. If a company’s inventory records are not accurate, it can lead to stockouts, overstocking, and other issues that can impact customer service and the overall efficiency of the supply chain.
Cycle counts can help companies identify discrepancies in inventory levels and address them before they become a bigger problem. This can help ensure that inventory is available when it is needed, without wasting resources on overstocking or tying up capital in excess inventory.
Conclusion
For companies that manage large amounts of inventory, cycle counts can be a valuable tool for improving accuracy, reducing shrinkage, and improving supply chain efficiency. By regularly counting a small subset of inventory, companies can identify and address potential issues before they become more serious problems. This can help ensure that inventory is available when it is needed, while also reducing waste and improving the bottom line.
How Does Cycle Counting Work?
Cycle counting is a way for businesses to regularly assess the accuracy of their inventory records. This process involves counting a small subset of an inventory on a frequent basis, instead of conducting a full physical inventory count once a year. The goal of cycle counting is to identify discrepancies in inventory records and take corrective actions. By implementing a cycle count program, businesses can improve inventory accuracy, reduce the likelihood of stockouts, and optimize working capital.
Types of Cycle Counts
There are different types of cycle counts that businesses can choose from based on their needs and resources. Here are three of the most common types:
- ABC Classification: This method prioritizes high-value, high-quantity, or frequently sold items for more frequent count, while low-value, low-quantity, or infrequently sold items get counted less often.
- Location-Based Counting: This method involves counting items in specific locations within a warehouse or store. This is useful when certain locations are more prone to errors or discrepancies than others, or when certain products are more frequently moved around.
- Cycle Count by Random Sample: This method involves randomly selecting a subset of items from the inventory and counting them. This is a cost-effective method as it does not require counting the whole inventory, and it can help identify discrepancies that are not detected in other methods.
The Cycle Counting Process
The actual cycle counting process involves several steps:
- Dividing Inventory: The inventory is divided based on the chosen type of cycle count (e.g. by ABC classification, by location, or by random sample). This ensures that all items are counted regularly, but not so frequently that it becomes disruptive to operations.
- Selecting Items: A subset of items is selected based on the criteria of the chosen cycle count method. For example, in an ABC classification cycle count, the high-value items will be counted more frequently than the low-value items.
- Counting Items: The selected items are physically counted and recorded. This is typically done with the help of handheld devices or barcode scanners to ensure accurate and efficient counting.
- Analyzing Discrepancies: Any discrepancies between the physical count and the inventory record are noted and analyzed. This helps identify the root causes of discrepancies, such as data entry errors, theft, or process issues.
- Correcting Discrepancies: Once the causes of discrepancies are identified, corrective actions should be taken. This can range from updating inventory records, to changing processes, or conducting additional training for employees.
After the first cycle count is completed, the cycle count program should be regularly reviewed and adjusted as needed. Based on the results of the cycle counts, the inventory accuracy can be improved, and the frequency or method of cycle count can also be readjusted.
Conclusion
Cycle counting is a valuable process for businesses to improve inventory accuracy. By following the cycle counting process, businesses can identify discrepancies, take corrective actions, and optimize working capital. By understanding the different types of cycle counts and selecting the appropriate method for their business needs, companies can achieve better control over their inventory and minimize stockouts.
Types of Cycle Counts
In inventory management, cycle count is a process of counting a small portion of inventory repeatedly throughout the year instead of an annual physical inventory count. It helps in ensuring inventory accuracy, identifying discrepancies, and preventing stock-out situations. The most common types of cycle counts are:
ABC Analysis
ABC analysis is one of the most popular methods used in inventory management. The ABC analysis classifies inventory into three categories based on their value or usage. This method believes that a small percentage of high-value items account for the majority of the inventory value and effort and hence should be prioritized for counting. The categories are:
- A category: 20% of the inventory items that account for 80% of the inventory value or usage. These items require the most attention and frequent counting.
- B category: 30% of the inventory items that account for 15% of the inventory value or usage. These items require moderate attention and periodic counting.
- C category: 50% of the inventory items that account for 5% of the inventory value or usage. These items require minimal attention and can be counted rarely.
ABC analysis helps in prioritizing the inventory count, focusing on high-value items, and avoiding unnecessary counting of low-value items. It also helps in identifying slow-moving and obsolete inventory that needs to be removed from the stock.
Random Sampling
Random sampling method selects a random sample of inventory items for counting. This method is usually used when there is no obvious pattern to follow, and items cannot be grouped by value or usage. It is helpful in situations where the inventory continuously fluctuates, new items are added, or old items become obsolete quickly.
Random sampling ensures that each item has an equal chance of being selected for counting, reducing the risk of inventory discrepancies. It also saves time and effort compared to counting all the items.
Using technology like barcode scanners or RFID tags, random sampling can be automated and streamlined. The system can randomly generate a list of items to count, send it to the warehouse operator, and track the progress in real-time.
Both ABC analysis and random sampling are effective methods of cycle counting and can be used in combination for maximum accuracy and efficiency.
In conclusion, cycle count is a crucial process in inventory management that helps ensure inventory accuracy, prevent stock-out situations, and maintain customer satisfaction. By using appropriate cycle counting methods like ABC analysis and random sampling, companies can improve their inventory control and reduce wastage, ultimately leading to increased profitability.
Benefits of Cycle Counting
Are you tired of spending countless hours conducting physical inventory counts? Do you wish there was a more efficient and accurate way to manage your inventory? Look no further than cycle counting. Cycle counting is a process by which a company regularly audits a portion of its inventory rather than counting all items at once. This method has become increasingly popular in recent years due to its numerous benefits.
1. Time and Cost Savings
Perhaps the most significant benefit of cycle counting is the time and cost savings it provides. Traditional physical inventory counts require shutting down operations, hiring additional staff, and often disrupting customer service. With cycle counting, inventory is audited in smaller, more manageable increments, eliminating the need for large-scale interruptions. This approach allows businesses to reduce the time and cost associated with traditional inventory counts significantly.
2. Improved Accuracy
Cycle counting also improves inventory accuracy. Regularly auditing a portion of inventory allows for faster identification of discrepancies and reduces the likelihood of significant errors going undetected for an extended period. Additionally, by conducting cycle counts more frequently, businesses can correct inventory discrepancies before they get out of hand, improving overall accuracy.
3. Optimize Stock Levels
Cycle counting allows businesses to optimize stock levels. By identifying inventory discrepancies quickly, it’s easier to determine optimal stocking levels for products. Understocking can lead to lost sales and unhappy customers, while overstocking can mean wasted resources. With cycle counting, companies can identify optimal stocking levels and fine-tune their inventory management systems accordingly.
4. Identify Process Improvements
Regular cycle counting helps businesses identify process improvements. By regularly auditing a portion of inventory, businesses can identify where errors occur and where processes can be made more efficient. This approach provides an opportunity for process improvements that can save time and reduce costs.
5. Compliance and Security
Cycle counting also helps companies stay compliant with regulations and ensures inventory security. Large-scale inventory counts can be a point of vulnerability, with employees, customers, or suppliers having been known to go missing. With smaller, more frequent audits, companies can keep track of inventory and ensure that compliance standards are being met.
In conclusion, cycle counting is an efficient and effective way to manage inventory. By conducting regular, smaller-scale audits, businesses can save time and money while increasing accuracy, optimizing stock levels, identifying process improvements, and ensuring compliance and security. If you’re looking to streamline your inventory management system, consider incorporating cycle counting into your operations.
Challenges with Cycle Counting
Cycle counting, though widely embraced by businesses for its numerous benefits, poses a significant number of challenges.
Time-consuming
Cycle counting is an ongoing process that requires consistent and even daily execution. Depending on the size of the inventory, cycle counting can take hours to complete, which can disrupt business operations, especially if the count is carried out during working hours.
Accuracy
The accuracy of cycle counting is crucial, as a single error could significantly impact inventory accuracy, leading to lost customers, inaccurate financials, and in some cases, regulatory violations. Achieving accuracy requires a stringent protocol, which often involves using multiple systems and specialized tools, which can be costly.
Data Integrity
Accurate data capture is critical to the cycle counting process. While most inventory management systems are equipped with barcode scanning and RFID technologies, errors can still occur where the technology fails to capture the required data accurately. Additionally, manual data entry by the counting staff poses another risk to data capture accuracy.
Employee Resistance
Introducing a cycle counting process can meet with employee resistance. Employees may view cycle counts as an additional task, which is time-consuming and detracts from their core functions. Moreover, employees whose performance is assessed based on inventory metrics may oppose the cycle counting process, fearing that their productivity may be adversely impacted by inaccurate metrics.
Training
Training employees on the cycle counting process is another significant challenge. With frequently changing technology and equipment, businesses must invest in training new employees and retraining existing ones regularly.
Frequency
Determining the appropriate frequency for cycle counting can be challenging. Too frequent counts can lead to disruptions, while insufficient counts may fail to capture inaccuracies and lead to lost revenue.
In conclusion, cycle counting is a crucial aspect of inventory management and offers numerous benefits to businesses. However, to achieve optimal results, businesses must overcome the challenges highlighted above through careful planning, rigorous execution, and consistent review of their inventory management systems.
Implementing Cycle Counting
Cycle counting is a process of physically counting inventory items on a routine basis to ensure the accuracy of inventory records. This can help companies identify inventory discrepancies, reduce inaccuracies, and improve inventory management practices. Implementing cycle counting requires careful planning and execution to achieve its intended benefits. Here’s a closer look at the steps involved in implementing cycle counting:
Assessing Inventory Categorization
The first step in implementing cycle counting is to assess inventory categorization. This means grouping inventory items into categories based on their characteristics, such as item type, value, usage frequency, and storage location. Companies should analyze their inventory data to identify the items that require the highest level of accuracy and prioritize them for cycle counting. This way, they can focus their efforts on the items that matter the most and avoid wasting time and resources on low-value or low-risk items.
Establishing Count Frequencies
The next step in implementing cycle counting is to establish count frequencies. This refers to how often companies should conduct cycle counts for each inventory category. The frequency depends on various factors such as item value, usage volume, storage location, and risk of loss or theft. For example, high-value items or frequently used items may require more frequent cycle counts to ensure their accuracy. Companies should also consider scheduling counts at the most suitable time, such as during slow periods or after shipments have been received.
Training Staff
The success of cycle counting largely depends on the people who perform it. Therefore, it’s crucial to train staff on the cycle counting process, including how to identify and reconcile discrepancies, use inventory management software, and follow proper safety and security procedures. Companies should also assign clear roles and responsibilities for cycle counting and provide adequate resources, such as counting tools and equipment, to ensure accurate and efficient counting.
Monitoring Results
After implementing cycle counting, companies should monitor the results to identify areas for improvement. They can measure the accuracy of inventory records, compare them with the cycle counting results, and track the frequency and timing of counts. This can help them identify patterns, such as high error rates in certain categories or locations, and take corrective actions to address them. Companies should also involve all stakeholders, such as managers, supervisors, and employees, in the monitoring process and use their feedback to refine the cycle counting process.
Implementing cycle counting can help companies ensure the accuracy of inventory records, reduce costs, and improve customer satisfaction. By following these steps, companies can implement an effective and efficient cycle counting program that delivers measurable benefits.