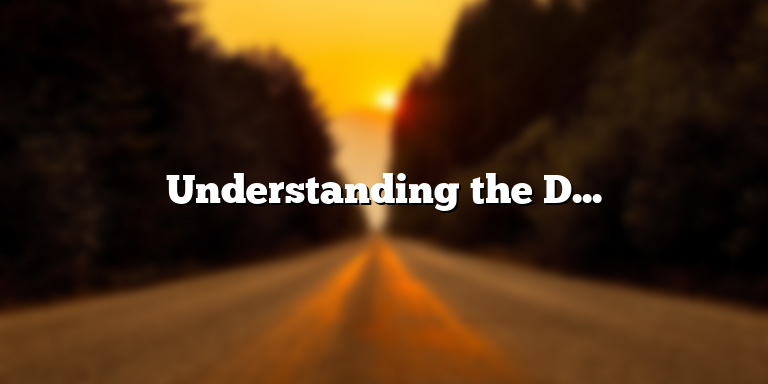
What is Cycle Counting?
Cycle counting is a crucial process that can help businesses maintain accurate inventory records and reduce the risk of discrepancies in their inventory levels. It involves counting a small portion of inventory on a regular basis, instead of counting everything at once, and making necessary adjustments to inventory records. The main objective of cycle counting is to ensure that inventory levels are accurate and consistent with the records.
Cycle counting is a proactive approach to inventory management that helps reduce costs associated with physical inventory counts such as labor, material, and equipment. It can also help identify potential inventory issues early on, enabling businesses to take corrective action before the issues become significant problems. One of the biggest advantages of cycle counting is that it helps prevent stockouts and overstocks, which can lead to lost sales, customer dissatisfaction, and financial losses.
The frequency of cycle counting can vary depending on the specific needs of the business. Some businesses may perform daily cycle counts, while others may do it weekly, monthly, or quarterly. The frequency of cycle counting is determined by the size of inventory, the rate of inventory turnover, and the level of accuracy needed. Regardless of the frequency, cycle counting should be done consistently and systematically to provide accurate and reliable inventory data.
A cycle count involves counting a small portion of inventory at a time, making it easier to manage and complete the inventory count accurately. Typically, only a portion of the inventory is counted at once, enabling businesses to maintain optimal inventory levels while still keeping a close eye on inventory accuracy. By counting a smaller portion of inventory regularly, businesses can identify and resolve inventory discrepancies before they become bigger problems.
Cycle counting can be performed manually or using automated inventory management systems. With manual counting, employees physically count the inventory and record the counts on a paper or spreadsheet. Automated systems use barcode scanners, RFID (Radio Frequency Identification) readers, or similar technology to scan inventory items and update inventory records automatically. Automated systems can significantly reduce the time and errors associated with manual cycle counting.
In conclusion, cycle counting is a vital process for managing inventory accurately and efficiently. With regular cycle counts, businesses can maintain optimal inventory levels, avoid stockouts and overstocks, reduce labor costs, and identify and correct discrepancies early. Through its proactive approach, cycle counting helps businesses stay on top of their inventory management game and stay competitive in today’s challenging market.
Why is Cycle Counting Important?
Cycle counting is a method of counting a specific portion of inventory on a regular basis, as opposed to performing a full physical inventory count all at once. This method of inventory management helps to identify discrepancies and inaccuracies in inventory records on an ongoing basis. Cycle counting is important because it allows businesses to maintain accurate inventory levels, which, in turn, leads to better decision-making and cost savings.
One of the primary benefits of cycle counting is that it helps to minimize disruptions in day-to-day operations. Traditional annual or semi-annual inventory counts can be a daunting and time-consuming task, requiring businesses to shut down operations and devote significant resources to counting inventory. On the other hand, cycle counting can be done incrementally over a period of time, allowing businesses to operate as usual while maintaining accurate inventory records. This allows for the proactive identification and correction of inventory discrepancies while minimizing operational interruptions.
Cycle counting also helps to identify patterns and trends in inventory discrepancies, which can be valuable information for businesses. By analyzing this data, businesses can identify areas of the warehouse or supply chain that may be contributing to the inaccuracies. They can then take steps to address these issues, such as optimizing inventory placement or adjusting procedures for receiving or issuing inventory. By doing so, businesses can improve overall efficiency and accuracy in inventory management.
In addition, cycle counting can be a valuable tool for preventing inventory shrinkage. This is particularly true when cycle counting is combined with other security measures, such as surveillance cameras or RFID technology. By maintaining accurate inventory records and taking steps to prevent shrinkage, businesses can reduce the cost associated with lost or stolen inventory items.
Conclusion
Cycle counting is an important method of inventory management that can help businesses maintain accurate inventory records and make better decisions. It allows for the proactive identification and correction of inventory discrepancies, while minimizing disruptions in day-to-day operations. By analyzing data obtained through cycle counting, businesses can identify areas for improvement in their inventory processes, leading to improved efficiency and cost savings.
Different Methods of Cycle Counting
Cycle counting is a common inventory management technique where inventory levels are regularly counted to identify and fix discrepancies between actual stock levels and recorded inventory levels. This ensures that inventory records are accurate, resulting in better inventory management processes and improved business performance. There are three primary methods of cycle counting: ABC analysis, Pareto analysis, and random sampling.
ABC Analysis
ABC analysis is a popular cycle counting method where inventory is categorized based on its value or importance to a business. The categories are usually A, B, and C, where A items have the highest value or importance, and C items have the lowest. This approach helps a business prioritize its inventory management efforts and focus on the most critical products or materials.
In this method, the items within each category are counted using different frequencies. For instance, A items – only 20% of inventory – may be counted on a weekly basis, while B items – 30% of inventory – may be counted every month. C items, which make up 50% of inventory, may be counted quarterly. This cycle counting method helps a business concentrate on the value of the items and the frequency of counting.
Pareto Analysis
Pareto analysis, also known as the 80/20 rule or the principle of imbalance, is another cycle counting technique based on a firm’s inventory. It assumes that a minority of your inventory has a massive influence on overall performance, so it focuses your attention and resources on that inventory.
The principle behind this type of cycle counting is that 80% of issues are typically caused by 20% of inventory issues. This method closely resembles ABC analysis but emphasizes the business’s inventory management priorities and focuses on identifying the typical issues affecting the inventory.
Random Sampling
Random sampling is a cycle counting method that involves the random selection of inventory items to be counted. Compared to other methods, random sampling is flexible and can be adapted to the company’s unique needs. The method only needs a predetermined sample size to produce an accurate representation of the whole inventory. Random sampling is ideal in situations where no prior knowledge of an inventory’s accuracy is available, making it an excellent approach for new or infrequently counted stocks.
Randomized cycle counting can be performed daily, weekly, or monthly, depending on the business’s size and needs. The frequency of counting also depends heavily on the inventory’s accuracy and location, with locations that have a higher degree of discrepancy requiring more frequent cycle counting exercises.
Conclusion
Inventory cycle counting is a necessary task for any business involved in the procurement and management of inventory. ABC analysis, Pareto analysis, and random sampling are the primary methods used in cycle counting, and any business can choose one that fits its needs. While each method of cycle counting has its advantages and disadvantages, businesses may choose to use a combination of methods to get the most accurate results possible in inventory management.
Benefits of Cycle Counting
Cycle counting is an inventory management technique that involves regularly counting a subset of your inventory. The goal is to ensure that inventory records are accurate and up to date. Rather than performing a full physical inventory count all at once, cycle counting involves counting a certain number of items on a rotating schedule. This approach offers several benefits that can help businesses significantly improve their inventory management processes.
Reduced Need for Full Physical Inventory Counts
One of the most significant benefits of cycle counting is that it reduces the need for full physical inventory counts. A full physical inventory count involves counting every item in the warehouse or inventory location. This process is time-consuming and requires a significant amount of resources. With cycle counting, businesses can count a smaller subset of items regularly, typically on a daily, weekly, or monthly basis, depending on the size of their inventory. This approach reduces the workload associated with full physical inventory counts and can help businesses save significant amounts of time and resources.
Improved Inventory Accuracy
Cycle counting is also an effective way to improve inventory accuracy. By regularly counting a smaller subset of items, businesses can identify and correct errors in their inventory records more quickly. This approach ensures that businesses have an accurate record of their inventory levels, which can help to prevent stockouts, overstocking, and other inventory-related issues. Accurate inventory records can also help businesses make more informed decisions about inventory management, purchasing, and other important business processes.
Cost Savings
Cycle counting can also help businesses save money by reducing the risk of lost or damaged inventory. By regularly counting a subset of items, businesses can identify and address inventory discrepancies quickly. This approach helps to prevent inventory shrinkage and can result in significant cost savings over time. Additionally, cycle counting can help businesses optimize their inventory levels, reducing the need for excess inventory and the associated costs.
Improved Customer Service
Cycle counting can also help businesses improve the quality of their customer service. By ensuring that inventory records are accurate and up to date, businesses can better meet customer demand, prevent stockouts, and fulfill orders more quickly and efficiently. This approach can help businesses to establish a solid reputation for reliability and customer satisfaction, which can lead to increased sales and customer loyalty.
Conclusion
Cycle counting is an effective inventory management technique that offers numerous benefits for businesses of all sizes. By reducing the need for full physical inventory counts, improving inventory accuracy, providing cost savings, and improving customer service, cycle counting can help businesses optimize their inventory management processes and improve their bottom line. Implementing a cycle counting program requires some initial investment in time, resources, and training, but the benefits of this approach are clear and can help businesses achieve long-term success.
Steps to Implement Cycle Counting
If you’re looking to improve inventory accuracy, implementing a cycle counting program can be a smart move. Cycle counting involves regularly counting a portion of your inventory instead of doing a full physical inventory count all at once. Here are the five steps you need to take to implement cycle counting in your operation.
Develop a Plan
The first step in implementing a cycle counting program is to develop a plan. Determine what areas of your inventory are the most important to count, how often you should count them, and who will be responsible for conducting the counts. You’ll also need to decide how you’ll handle discrepancies found during the counting process and how you’ll track the results of each cycle count.
Set Up a Schedule
Once you have a plan in place, it’s time to establish a schedule for your cycle counts. Depending on the size of your inventory and the frequency of your sales, you may want to count certain items on a daily, weekly, or monthly basis. You can use your sales data to help you determine the most appropriate schedule for your operation. It’s better to keep schedule flexible, according to requirements.
Train Employees
Your cycle counting program will only be successful if your employees are properly trained to conduct the counts. Make sure they understand the importance of inventory accuracy, how to conduct a cycle count, and how to report discrepancies. You may want to provide training in small groups to ensure everyone is comfortable with the process.
Conduct Cycle Counts
With your schedule and employee training in place, it’s time to start conducting cycle counts. During a cycle count, a small number of items in a designated area of your warehouse are counted to check for any discrepancies between the physical count and your inventory records. If discrepancies are found, you’ll need to investigate the cause and make any necessary adjustments to your records.
Analyze Results
Finally, you need to analyze the results of your cycle counting program to determine whether it’s helping to improve accuracy in your inventory records. Keep track of the number and type of discrepancies that are found during each count and look for patterns or trends that may indicate a larger issue. Use this information to make changes to your cycle counting program as needed to ensure continual improvement.
Implementing a cycle counting program requires careful planning and consistent effort, but the benefits are well worth it. With accurate inventory records, you’ll be better equipped to make informed decisions about your business and provide your customers with the products they need in a timely manner.
Challenges Faced with Cycle Counting
Cycle counting is a crucial process in inventory management that helps organizations maintain accurate inventory records and reduce errors. With cycle counting, inventory is counted on a rotating basis, rather than using a traditional physical inventory count. This helps ensure that inventory is always up-to-date and accurate, making it easier for businesses to make informed decisions about their inventory stock levels and purchasing needs. However, cycle counting can present its own unique set of challenges. These typically include employee resistance, lack of proper training, and difficulties in establishing a proper counting protocol.
One of the main challenges faced with cycle counting is employee resistance. Many employees may not have a clear understanding of the importance of cycle counting, and may see it as an unnecessary task that takes away from other job responsibilities. In some cases, employees may feel that cycle counting is a waste of time and does not add any value to the organization. This can make it difficult for managers to get employees to commit to the process and carry out their responsibilities effectively.
Lack of proper training can also present a challenge when it comes to cycle counting. Employees may not have the necessary skills or knowledge to carry out the process effectively, which can result in inaccurate counts and errors. This can lead to inventory discrepancies that can take a significant amount of time and resources to correct, which can ultimately impact the bottom line. Proper training is essential in ensuring that employees understand the counting process, know how to use the tools involved, and are able to carry out their responsibilities effectively.
Another challenge faced with cycle counting is difficulties in establishing a proper counting protocol. Each organization may have its own unique requirements when it comes to cycle counting, and it can be difficult to establish a standardized process that works for everyone. This can make it challenging to ensure that all inventory is being counted accurately and according to the organization’s specific requirements. A well-established counting protocol is essential in ensuring accurate and consistent results.
In conclusion, cycle counting is an essential process in inventory management that helps organizations maintain accurate inventory records and reduce errors. However, challenges such as employee resistance, lack of proper training, and difficulties in establishing a proper counting protocol can make the process difficult to carry out effectively. By addressing these challenges, organizations can ensure that their cycle counting process is accurate, reliable, and streamlined, ultimately leading to better business outcomes.
What is cycle counting?
Cycle counting is a method of inventory management in which a portion of a company’s inventory is counted on a regular basis instead of counting everything once a year. In this way, companies can continually monitor their stock levels and ensure the inventory records and physical inventory match, without having to shut down operations for a full physical inventory count.
Why is cycle counting important?
Cycle counting helps organizations avoid inaccurate inventory records and stock-outs or overstocking of products. The process also catches inaccuracies in receiving, shipping, and recording inventory. By consistently counting a portion of the inventory, organizations can optimize warehouse operations and improve inventory accuracy over time. It ultimately saves companies time and resources that would have been wasted in a full physical inventory count.
Types of cycle counting
There are several types of cycle counting depending on the needs of the organization:
- ABC Analysis: This method categorizes inventory into different groups based on the value or level of importance. Class A items would then be counted more frequently than Class C items since they’re the most important.
- Random Sampling: With this method, a portion of the inventory is randomly selected for counting without following a specific pattern or schedule.
- Threshold Counting: This method entails counting only when inventory levels reach a specific threshold. For example, when the inventory levels of a specific item reach a minimum level, cycle counting can be triggered to ensure there is enough stock.
- Cycle by Location: For this method, a portion of the inventory located in a specific warehouse or location is counted during each cycle count.
Implementing cycle counting
Organizations looking to implement cycle counting should start with an analysis of their inventory and warehouse operations. They should also determine the ideal cycle counting frequency and method for their inventory. Once this is established, the cycle counting process should be standardized and documented to minimize errors.
It’s also essential to train staff on the process and provide ongoing support to ensure accuracy. Depending on the size and complexity of the inventory, organizations may choose to use technology like barcode scanning or radio-frequency identification (RFID) to improve the efficiency and accuracy of the cycle counting process.
Benefits of cycle counting
Cycle counting has many benefits for organizations. For one, it helps minimize the need for full physical inventory counts which can be time-consuming and disruptive to business operations. It also ensures inventory accuracy which is crucial for making sound business decisions and fulfilling customer orders. Furthermore, cycle counting increases efficiency by identifying and addressing issues in inventory management. It also helps minimize the risk of stock-outs and overstocking of products which can improve the company’s bottom line.
Conclusion
Overall, cycle counting is a crucial component of inventory management that helps companies improve accuracy, save time, and reduce the need for full physical inventory counts. With accurate inventory records and efficient operations, companies can improve their financial performance while serving their customers effectively. Organizations should assess their inventory needs and implement the appropriate cycle counting method to take advantage of the benefits offered by this process.