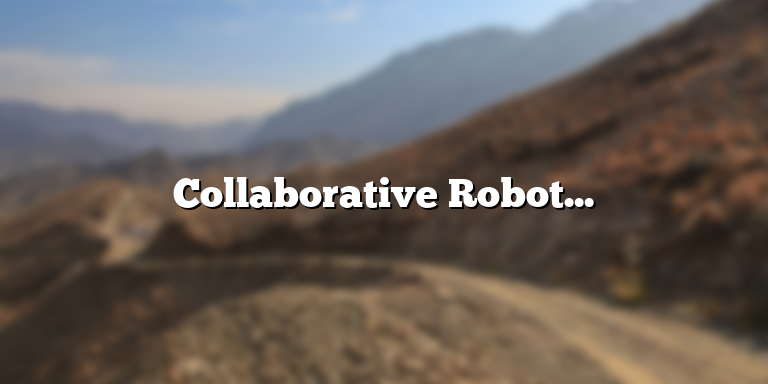
What Are Collaborative Robots?
Collaborative robots, often referred to as cobots, are a relatively new concept in the world of automation. Unlike traditional robots, cobots are designed to work alongside humans in a safe and efficient manner without the need for safety barriers or cages. Essentially, cobots are designed to collaborate with operators, rather than replace them. This makes them an attractive option for a range of industries, from manufacturing and logistics to healthcare and service industries.
One of the key advantages of cobots is their versatility. Unlike traditional robots that are often designed for a specific task, cobots are modular and can be easily programmed and adapted for a range of tasks. This means that they can be used in a variety of different settings and applications, from assembly line operations and material handling to pick-and-place tasks and quality control.
In addition to their flexibility, cobots are also highly adaptable in terms of their size and shape. They can be designed to fit into tight spaces and work in close proximity to human operators, making them ideal for use in smaller factories and workshops. They can also be customized to suit specific tasks and applications, with a range of end-effectors, sensors, and grippers available to enable them to perform a wide range of operations.
When it comes to safety, cobots are designed to operate in a collaborative environment with humans, which means that they have built-in safety features that allow them to detect and respond to the presence of humans in their workspace. This allows them to operate safely alongside human colleagues, without the need for safety barriers or cages that can restrict access and reduce efficiency.
Overall, collaborative robots are a promising development in the automation industry, offering a range of benefits in terms of safety, efficiency, and adaptability. As technologies continue to evolve and improve, it is likely that cobots will become an increasingly common sight in workplaces around the world.
The History of Collaborative Robots
Collaborative robots, also known as cobots, were first conceived in the 1990s by J. Edward Colgate, a roboticist from Northwestern University. Cobots are robots designed to work in conjunction with human workers, performing repetitive or dangerous tasks to make the work environment safer and more efficient.
Before cobots, traditional robots were often large and heavy, requiring a lot of space and safety measures to avoid potential accidents. Cobots, on the other hand, are smaller and lightweight, making them easier to maneuver and integrate into existing production lines. They are also designed with safety features, such as sensors and stop mechanisms, that allow them to work alongside human operators without posing a risk.
Initially, cobots were not widely adopted due to their relatively high cost and limited capabilities. However, with advancements in technology and decreasing costs, cobots have become more accessible and versatile in recent years.
One of the earliest examples of a cobot was the PUMA (Programmable Universal Machine for Assembly), developed in the 1980s by Unimation, a division of Westinghouse. Though not designed specifically as a cobot, the PUMA was able to safely work alongside human workers due to its speed and accuracy.
In the early 2000s, Danish manufacturer Universal Robots launched the UR5, one of the first cobots designed for industrial use. The UR5 was small enough to fit on a workbench and could be programmed by non-technical users, making it an appealing option for small and mid-sized companies.
Since then, many other companies have entered the market, offering a range of cobots with varying payloads, reach, and applications. Cobots have been widely adopted in industries such as food and beverage, automotive, and electronics manufacturing, where they can perform tasks such as pick-and-place, soldering, and machine tending.
As technology continues to improve, cobots are poised to become an even more integral part of the workforce. With their ability to automate repetitive and dangerous tasks, cobots can help improve productivity and increase workplace safety. The future of collaborative robotics is bright, and it will be exciting to see the ways in which they continue to evolve and transform various industries.
The Advantages of Collaborative Robots
Collaborative robots, also known as cobots, are advanced robots designed to work alongside humans in various manufacturing operations. Apart from their impressive features and capabilities, they have several advantages over traditional robots when it comes to safety and flexibility. Here are some of the most significant advantages of collaborative robots:
Safety
One of the primary reasons that make cobots more preferred than traditional robots is the advanced safety features they come with. Collaborative robots are designed to interact safely with humans, and they are equipped with sensors and cameras that detect when a human is in close proximity. This feature ensures that the robot stops immediately it senses that a person may be in danger. Additionally, since cobots are not as heavy as traditional robots, the possibility of causing injury or damage to someone or something in the workplace is considerably minimized.
With traditional robots, it is necessary to have guarding or cages surrounding them, which considerably decreases the amount of workspace available. The guarding also makes it difficult for the operators to communicate with their colleagues, which can cause complications and reduce productivity. Collaborative robots, on the other hand, have easy-to-use control software that allows the operators to teach and train the robots with ease. As a result, the cobots can work alongside humans, enhancing overall efficiency and productivity, without causing safety concerns.
Flexibility
Another primary advantage of collaborative robots is flexibility. Traditional robots are designed for a specific task and require extensive programming to have them perform something different. On the other hand, collaborative robots are incredibly versatile and can adapt to different tasks easily. Cobots can switch quickly and easily from one task to another, allowing operators to maximize their production output without changing the robot’s physical components or requiring technical support.
With cobots, operators can reprogram and recalibrate the robot in just a few hours. By doing this, they can use the same robot for different operations, increasing production capacities and lowering the overall costs involved. This enhanced flexibility makes collaborative robots ideal for small and medium-sized enterprises seeking to increase their productivity output without investing large amounts of resources.
Cost-Effective
Collaborative robots are also known to be cost-effective, making them a preferred choice for businesses of all sizes. Compared to traditional robots, which require extensive technical skills and maintenance, cobots are relatively easy to set up, program, and maintain. The hardware and software of cobots are often intuitive and straightforward to use, making them more accessible for businesses that do not have advanced technical skills. Additionally, since they have increased safety features, traditional guarding is not necessary, saving on additional costs, and the need to employ additional safety personnel.
In conclusion, collaborative robots have several remarkable advantages over traditional robots. Increased safety and flexibility capabilities, as well as being cost-effective, make cobots ideal for a wide range of businesses and manufacturing operations. These advantages have led to rapid growth in the cobot market, with more and more companies turning to cobots to reduce their production costs while increasing their overall efficiency.
The Disadvantages of Collaborative Robots
Collaborative robots, also known as “cobots,” are robots designed to work alongside humans in shared workspaces. While cobots have gained popularity due to their ease of use and versatility, they do come with some disadvantages that need to be considered before investing in this type of automation technology.
One disadvantage of collaborative robots is their higher cost compared to traditional industrial robots. Cobots are designed to be easy to program and to work safely alongside human workers. This requires advanced sensors and software, which often means a higher price tag. In addition, cobot manufacturers may charge more for ongoing maintenance and support, which can also increase the total cost of ownership.
Another disadvantage of collaborative robots is their lower payload capacity. Due to safety concerns, cobots are designed to have a lower maximum payload than traditional industrial robots. This means that they may not be suitable for certain tasks that require heavy lifting or extensive reach. In addition, the lower payload capacity may limit the types of tools and end-effectors that can be used with a cobot.
Another potential disadvantage of collaborative robots is the need for more frequent programming and set-up. Unlike traditional robots that are often programmed once and then run for long periods of time, cobots may need to be reprogrammed and reconfigured more frequently as work tasks change or new products are introduced. This can add additional time and cost to the implementation and operation of cobots in a manufacturing environment.
In addition, cobots may not be the best choice for every manufacturing application. While they can be highly effective for certain tasks, there may be situations where a traditional industrial robot is more appropriate. For example, if a manufacturing process requires high-speed or precision movements, a traditional robot with a higher payload capacity and faster cycle times may be a better choice.
Finally, safety concerns must always be considered when working with collaborative robots. While cobots are designed to be safe for human workers to operate alongside, accidents and injuries can still occur if proper safety protocols are not followed. This includes training workers on how to safely interact with cobots, as well as ensuring that cobots are properly guarded and that all safety features are functional.
Overall, while collaborative robots offer many benefits for manufacturers looking to automate their processes, it’s important to carefully consider the potential disadvantages before investing in this technology. Understanding the limitations of cobots and selecting the right automation solution for each manufacturing task is key to achieving optimal efficiency and productivity.
The Different Types of Collaborative Robots
Collaborative robots, also known as cobots, are designed to interact with humans in a shared workspace. Unlike traditional industrial robots that require caged environments for safety, collaborative robots can work alongside humans safely and efficiently.
There are four main types of collaborative robots:
1. Power and Force Limited Robots
Power and force limited (PFL) robots are designed to limit their power and force output, making them safe to work with even without additional safety measures. These robots use torque sensors and safety software to detect any accidental impact or collision and immediately act to prevent injury. PFL robots are best suited for high force or high-speed applications.
These robots have flexible joints that allow them to move and adapt to the position of the operator. PFL robots come in different sizes and weight categories, which make them ideal for a wide range of applications.
2. Safety-Rated Monitored Stop Robots
Safety-rated monitored stop (SRMS) robots are designed to stop immediately upon detecting the presence of humans in their workspace. The safety-rated system is used to monitor the robot’s status and the presence of the operator. These robots come with a variety of safety features, including fencing, safety mats, and light curtains.
SRMS robots are ideal for manufacturers or production lines where humans and robots work in close proximity. These systems can also be used in hazardous environments where humans are not safe to work.
3. Hand Guiding Robots
Hand guiding robots are designed to be manually trained by operators using their hands to guide the robot’s movement. This allows the robot to learn specific tasks and movements and repeat them accurately and efficiently. Hand guiding robots are generally smaller in size and weight, making them ideal for precision applications that require low force and delicate manipulation.
These robots are well suited for repetitive and delicate tasks like intricate assembly, polishing, and testing. Hand guiding robots can be programmed to work in collaboration with humans to increase productivity and optimize the manufacturing process.
4. Speed and Separation Monitoring Robots
Speed and separation monitoring robots (SSMR) are designed to operate at high speed while safely detecting the presence of humans or obstacles in their workspace. SSMR robots use sensors and scanners to detect humans or other possible obstacles and react accordingly, either by slowing down or stopping.
These robots are typically used in manufacturing floors with high-speed operations. They can work safely with humans and can improve the efficiency and productivity of the production line. SSMR robots can be used in assembly lines, packaging, or pick-and-place applications.
Collaborative robots play a key role in the automation of manufacturing processes. They provide manufacturers with the flexibility and safety needed to optimize production lines while also keeping the operators safe. By understanding the different types of collaborative robots and their applications, the right cobot can be selected to increase production efficiency and safety.
Process improvement is necessary for incorporating collaborative robots in the production line effectively.
Applications of Collaborative Robots
As the demand for automation continues to grow, one technology that is widely used in industries is collaborative robots. Collaborative robots, also known as cobots, are designed to work alongside human workers, aiding them in their tasks, and ultimately improving productivity and safety. Below are some examples of how cobots are being used in various industries:
Manufacturing
Collaborative robots have been a game-changer in manufacturing, especially in industries that involve repetitive tasks, such as assembly lines. Cobots can pick and place products, weld, and paint, among other tasks, with precision, speed, and accuracy. Additionally, cobots can work 24/7, increasing productivity, while minimizing the risk of human error and injuries.
Healthcare
The healthcare industry is also making use of collaborative robots, especially in tasks that require precision and accuracy, such as surgery. Cobots are designed to work with surgeons, aiding them with tasks such as holding a tissue in place or suturing a wound. Collaborative robots are also used in the production of medical devices, where precision is crucial to the safety of patients.
Agriculture
Collaborative robots have also found their way into the agricultural sector. Cobots can be programmed to pick fruits and vegetables, weed, and plant. They can work tirelessly, day and night, increasing productivity and minimizing the risk of injury to human workers.
Logistics
Cobots are also being used in the logistics industry. Collaborative robots can help with tasks such as packing, sorting, and shipping. They can work alongside human workers, increasing productivity, and minimizing the time required to complete tasks.
Education
Collaborative robots are not just for industries, but also for education. Cobots are being used in schools and universities to teach students about programming, robotics, and automation. Collaborative robots are programmed to interact with students, teaching them how to program, troubleshoot, and maintain cobots.
Entertainment
Collaborative robots are also being used in the entertainment industry. Cobots are programmed to work with performers, creating impressive shows and performances. Collaborative robots can move, dance, and sing alongside human performers, enhancing the entertainment experience for the audience.
Collaborative robots are an excellent example of how technology can work alongside humans to achieve better results. As the demand for automation continues to grow, it is expected that more industries will adopt collaborative robots as a way of improving productivity, efficiency, and safety.
Collaborative robot definition is essential for understanding the latest advances in robotics technology.
What are Collaborative Robots?
Collaborative robots, also known as cobots, are robots that work alongside humans in a shared workspace. They are designed to be safe, flexible and easy to use and can perform repetitive or dangerous tasks that would otherwise require human intervention.
The Advantages of Collaborative Robots
One of the main advantages of collaborative robots is that they can improve the efficiency of a work process. They are designed to work alongside humans and can take on repetitive and dangerous tasks, freeing up the workers to focus on more complex and creative tasks. Cobots can also carry out tasks that require high precision or that are difficult for humans to perform, such as working in confined spaces or with hazardous materials. This results in increased productivity and safety for workers.
Another advantage of cobots is that they are easier to program than traditional industrial robots. This means that they can be set up and reconfigured quickly, without the need for specialized programming knowledge. Cobots can be trained by workers to perform specific tasks, which makes them ideal for smaller companies or for businesses that need flexibility in their production processes.
The Disadvantages of Collaborative Robots
One of the main disadvantages of collaborative robots is their cost. Cobots can be more expensive than traditional industrial robots, especially when considering their safety features and sensors. However, the cost of cobots is dropping as they become more widespread, and their benefits often outweigh the initial investment.
Another potential disadvantage of cobots is their limited strength and payload capacity. Collaborative robots are designed to work alongside humans and are not usually capable of lifting and carrying heavy loads. However, this limitation can be overcome by integrating cobots with other machines or by using multiple cobots in a team to carry out heavy tasks.
The Applications of Collaborative Robots
Collaborative robots are finding increasing applications in a wide range of industries, including manufacturing, logistics, healthcare and agriculture. In manufacturing, cobots can be used to assemble parts, pack and palletize products or perform quality control checks. In logistics, cobots can be used to move and sort goods, while in healthcare they can assist with tasks such as patient care and medication dispensing.
In agriculture, cobots can be used to perform tasks such as planting, weeding and harvesting. They can also be used to monitor crops and collect data on crop health and growth. The potential applications of cobots are limited only by our imagination, and it is likely that we will see many more innovative uses of collaborative robots in the years to come.
The Future of Collaborative Robots
The future of collaborative robots is exciting and full of possibilities. With advances in artificial intelligence and machine learning, we can expect to see cobots that are even more intelligent and autonomous, able to perform complex tasks with minimal human intervention. We may also see cobots that are capable of learning from their human co-workers and adapting to new situations and environments.
Another area of development for cobots is in the field of human-robot collaboration. Researchers are exploring ways to improve the interaction between humans and robots, for example by developing exoskeletons that allow humans and robots to work together more seamlessly. This opens up the possibility of new applications for cobots, such as in space exploration or disaster relief.
As we continue to develop and improve collaborative robots, it is likely that they will become even more integrated into our daily lives and work processes. While there may be challenges to overcome, such as ensuring the safety of humans working alongside cobots, the potential benefits are immense. Collaborative robots have the power to transform the way we work, making our lives easier, safer and more productive.
Services in economics plays a crucial role in understanding the use of collaborative robots in industries and businesses.